For detailed information, other images and documents, please select individual articles from the following table.
SMP adhesive sealant XTREME
Elastic SMP-based adhesive and sealant for large bonded areas and with high temperature resistance
Register now and access more than 125,000 products








Variants
Register now and access more than 125,000 products
Long skin formation time
- Ideal for large areas
- Joint parts can be repositioned
- Allows complex components to be bonded and sealed
Short-term high temperature resistance
Suitable for powder coatings
Many areas of application
- Good adhesion properties on a variety of surfaces
- Good UV stability and weather resistance outdoors
- Not corrosive to metals
- Suitable for bonding and sealing in food processing plants (ISEGA)
Elastic adhesive joint
- Compensates for expansions in different materials
- Dampens vibrations and noise
- Easy to smooth
Can be sanded and painted
- The adhesive can be painted over with most standard paints and lacquers when hardened
- Ready to sand after complete curing
Chlorine-resistant/disinfection concentration (not suitable for permanent underwater use in swimming pools)
Compatible with natural stone
Solvent and silicone-free
Our products featuring the EMICODE label are low emission/environmentally compatible. The EMICODE classification system awards labels to construction products that comply with the very stringent health and environmental requirements of recognised institutes.
ISEGA: Can be used in food-processing areas, e.g. for bonding wall and floor areas in food processing and handling companies. Clearance certificate no.: 42178 U16
EMICODE EC1plus: Very low emissions - the EMICODE classification system indicates the environmental and health compatibility of construction products. Low-emission products bear the EC1plus label.
- Store original container tightly sealed in a dry place at temperatures between +15°C and +25°C without exposure to direct sunlight.
- Will not adhere to polyolefins (including PE, PP) without pre-treatment e.g. plasma or corona treatment.
- When bonding to PVC, ABS, hard PS, concrete and powder-coated surfaces, priming with AdhesionPlus for plastic/wood/stone (art. no. 0890 100 62) is
- recommended.
- When joining non-absorbent materials (moisture content of material ≤ 8 %), the adhesive must also be finely misted with water in order for the adhesive to fully cure.
- The bonded workpieces should not be coated until after the adhesive is fully hardened; if they are coated too early, the formation of bubbles in the coating cannot be ruled out.
The long-term behaviour of bonds between materials with different linear expansion rates must be evaluated, in particular when placed under load in areas with variable temperatures
- No general statement can be made concerning the wettability or bonding ability of anodised surfaces due to the variety, age and potential additional treatments on these adhesive surfaces, such as oils or waxes.
- Due to aluminium surfaces and properties being difficult to define, we always recommend that you obtain sufficient information from the supplier to enable you to choose the optimum pre-treatments for your particular bonding application. Sufficient preliminary tests are necessary.
- In the production and processing of stainless steel, auxiliary materials such as wax, oils, etc. are frequently used. These materials usually cannot be simply wiped clean. It has been shown that cleaning with universal cleaner type 60 (art. no. 0892 130 030, 0892 130 031), sanding or (preferably) sandblasting the surface, followed by repeated cleaning with solvent delivers considerably better bonding results.
- In principle, zinc-plated sheet metal must always be protected against ongoing ingress of moisture to prevent "white rust formation". This includes preventing any moisture that arises from coming into contact with the bonding surface.
- The sealant will not reliably adhere to powder coatings that contain PTFE without pre-treatment (e.g. plasma treatment).
- PMMA must only be glued when it is not under tension; otherwise, stress cracks are likely to occur.
- The current version of the Technical Guidelines for the Glazing Industry No. 11 must be observed for mirror bonding.
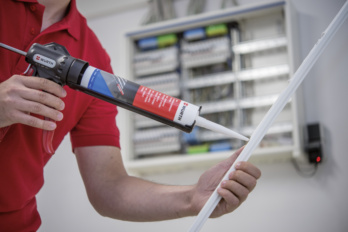
SMP adhesive sealant | SMP UNIVERSAL 0893237100 0893237101 0893237102 | SMP SPRINT 0893237120 0893237121 0893237122 | SMP XTREME 0893237130 | SMP HIGH TACK 0893237140 | SMP CLEAR 0893237152 | SMP METALLIC 0893237160 | SMP 2C 0893237170 | |
Rubber | - | - | ⎷1 | - | - | - | ⎷1 | |
Rigid foams | - | - | ⎷ | - | - | - | ⎷ | |
Neoprene | - | - | ⎷1 | - | ⎷ | - | ⎷1 | |
PE/PP | - | - | - | - | - | - | - | |
PMMA | - | ⎷ | ⎷1 | - | ⎷ | - | ⎷1 | |
Polyamide | - | ⎷ | ⎷2 | - | - | - | ⎷2 | |
Polycarbonate | - | ⎷ | ⎷1 | - | ⎷ | - | ⎷1 | |
Polystyrene | - | ⎷ | ⎷1 | - | ⎷ | - | ⎷1 | |
PTFE | - | - | - | - | - | - | - | |
PU | ⎷ | - | ⎷ | ⎷ | ⎷ | - | ⎷ | |
PVC | ⎷ | ⎷1 | ⎷1 | ⎷ | ⎷ | - | ⎷1 | |
Silicone | - | - | - | - | - | - | - | |
Styrofoam | - | ⎷ | ⎷ | - | ⎷ | - | ⎷ | |
Painted surfaces | Painted surfaces | - | ⎷ | ⎷ | - | - | - | ⎷ |
Wood and wood materials | Decorative panels | ⎷ | ⎷ | - | ⎷ | - | - | - |
Wood, MDF (chipboard) | ⎷ | ⎷ | ⎷ | ⎷ | ⎷ | - | ⎷ | |
Cork | - | ⎷ | ⎷ | ⎷ | ⎷ | - | ⎷ | |
Laminated panels | ⎷ | ⎷ | ⎷2 | ⎷ | ⎷ | - | ⎷2 | |
Stone and construction materials | Concrete | ⎷ | ⎷ | ⎷1 | ⎷ | ⎷ | ⎷ | ⎷1 |
Bituminous surfaces | - | - | - | - | - | - | - | |
Aerated concrete, gypsum, gypsum plasterboard | ⎷ | ⎷ | ⎷1 | ⎷ | ⎷ | ⎷ | ⎷1 | |
HPL | ⎷ | ⎷ | ⎷2 | ⎷ | ⎷ | - | ⎷2 | |
Artificial stone | ⎷ | ⎷ | ⎷2 | ⎷ | - | ⎷ | ⎷2 | |
Natural stone | - | ⎷ | ⎷ | - | - | - | ⎷ | |
Stone | ⎷ | ⎷ | - | ⎷ | - | ⎷ | - | |
Cement fibreboards | ⎷ | ⎷ | ⎷1 | ⎷ | ⎷ | - | ⎷1 | |
Other | Enamel | ⎷ | ⎷ | ⎷2 | ⎷ | ⎷ | ⎷ | ⎷2 |
Glass | ⎷ | ⎷ | ⎷ | ⎷ | ⎷ | ⎷ | ⎷ | |
Fibre glass | - | ⎷ | ⎷ | - | ⎷ | - | ⎷ | |
Mirror | - | - | ⎷2 | ⎷ | ⎷ | - | - | |
Porcelain, ceramic, tiles | ⎷ | ⎷ | ⎷2 | ⎷ | ⎷ | ⎷ | ⎷2 | |
Paper | - | - | ⎷ | - | ⎷ | - | ⎷ | |
Cardboard | - | - | ⎷ | - | ⎷ | - | ⎷ | |
Mesh | - | - | - | - | ⎷ | - | - | |
Leather | - | - | ⎷ | - | ⎷ | - | ⎷ | |
Metal | Aluminium | ⎷ | ⎷ | ⎷2 | ⎷ | ⎷ | ⎷ | ⎷2 |
Lead | ⎷ | ⎷ | ⎷2 | ⎷ | ⎷ | ⎷ | ⎷2 | |
Stainless steel | ⎷ | ⎷ | ⎷2 | ⎷ | ⎷ | ⎷ | ⎷2 | |
Copper | ⎷ | ⎷ | ⎷2 | ⎷ | ⎷ | ⎷ | ⎷2 | |
Brass | ⎷ | ⎷ | ⎷2 | ⎷ | ⎷ | ⎷ | ⎷2 | |
Steel/iron | ⎷ | ⎷ | ⎷2 | ⎷ | ⎷ | ⎷ | ⎷2 | |
Zinc | ⎷ | ⎷ | ⎷2 | ⎷ | ⎷ | ⎷ | ⎷2 | |
Plastic | ABS | ⎷ | ⎷ | ⎷1 | ⎷ | - | ⎷ | ⎷1 |
GRP | ⎷ | ⎷ | ⎷2 | ⎷ | - | ⎷ | ⎷2 | |
1. Prime with AdhesionPlus P/W/S (art. no. 0890 100 62) 2. Pre-treat with cleaner type 60 (art. no. 0892 130 030, 0892 130 031) 3. Pre-treat with cleaner type 20 (art. no. 0892 100 11) |
Optimisation table: | ||
Surface/material | Optimisation steps* | Notes |
(PES, EP/PES) | ||
2-component top-coat, water- or solvent-based (PUR, acrylic) | Universal cleaner type 60 | Due to the large number of paints available, this information is only a guide. Where necessary, perform preliminary tests. |
2-component primers, water or solvent-based | Universal cleaner type 60 | Due to the large number of primers, this information is only a guide. Where necessary, perform preliminary tests. |
(PUR, acrylic, epoxy resin) | ||
Cathodic dip coating | Universal cleaner type 60 | – |
(E-coating) | ||
Coil-coat coating | Universal cleaner type 60 | – |
ABS | AdhesionPlus primer for P/W/S | – |
GFRP (unsaturated polyester), gelcoat side or SMC | 1. Basic cleaning with universal cleaner type 60 2. Sand with "very fine" or grain 60-80 abrasive fleece and then vacuum. 3. Post-cleaning with universal cleaner type 60 | Adhesive surface must be protected against UV radiation (opaque cover). |
Rubber | AdhesionPlus primer for P/W/S | – |
PMMA | AdhesionPlus primer for P/W/S | – |
Polyamide | Universal cleaner type 60 | – |
PVC, hard PVC, hard PS | AdhesionPlus primer for P/W/S | – |
Wood, plywood, MDF, wood products and cork | Dedusting | – |
HPL laminated panels (Resopal, Ultrapas) | Universal cleaner type 60 | – |
Enamel, porcelain, ceramic, tiles | Universal cleaner type 60 | Due to the large number of substrates available, this information is only a guide. Where necessary, perform preliminary tests. |
Mirror | Anti-static plastic cleaner type 20 | See Page 3 for detailed instructions on mirror bonding. |
Concrete, mineral mortar, plaster and cement fibre board | AdhesionPlus primer for P/W/S | – |
Synthetic stone (Corian, Varicor) | Universal cleaner type 60 | – |
Anodised aluminium | Universal cleaner type 60 | – |
Aluminium (AlMg3, AlMgSi1) | 1. Basic cleaning with universal cleaner type 60 2. Sand lightly with a very fine abrasive fleece 3. Post-cleaning with universal cleaner type 60 | – |
Non-ferrous base metals (brass, copper, bronze, etc.) | – | |
Stainless steel (rustproof) | – | |
Steel (St 37 etc.) | – | |
Zinc-plated steel (hot-dip or zinc-plated) | – | |
Zinc | Formation of white rust, in the presence of moisture | |
Powder coatings | AdhesionPlus primer for P/W/S | AdhesionPlus for P/W/S must be used. |
* Follow the corresponding sequence of the individual steps |
Ideally suited for vehicle, bodywork, caravan and container construction, ventilation and air-conditioning technology, the building trade, various areas of industry, shipbuilding and for metal, apparatus and plant construction, the paper industry or applications in pharmaceutical, food and beverage industries according to ISEGA certificate*, etc.
Possible applications include assembly connections, skirting boards, laminate laying, cable ducts, stair construction, bonding of façades, (cassette) sandwich elements, glass bonding in furniture and display case construction, solar and wind energy systems, sign attachment, mirrors in accordance with DIN EN 1036 for walls and doors.
The application surfaces must be clean, dry and free of grease. For pre-treatment, please refer to the optimisation table in the technical data sheet.
Cut off thread cap, screw on nozzle and cut to the required width. Apply the adhesive using a suitable application gun. Apply adhesive in vertical beads at intervals of 30 cm.
The workpieces must be joined within the skin formation time. Fasten/press the parts together after joining until the functional strength is reached.
Mirror bonding:
The length of the applied beads should not exceed 200 mm. The distance between the beads should be approx. 200 mm. Apply the adhesive in VERTICAL beads. Mount the mirror within 10 to 15 minutes after applying the adhesive and press on firmly. The mirror must be fixed tension-free for at least two days.
For more information, please refer to the technical data sheet.
Select RAL-colour code
!! NOTE: On-screen visualisation of the colour differs from real colour shade!!