Cement repair filler CERAfix® 202
Cement repair filler CERAfix 202 stable
FILR-(CERAFIX-202)-25KG
CERAFIX


Register now and access more than 125,000 products
Long-lasting application
- Suitable for floors, walls and ceilings
- Does not slide on vertical surfaces
Quick-setting
- Reduces downtimes
- Fast build-up of layers
Low tension and shrinkage
- Fast curing
- Quick to reach maturity
Simple and excellent application
Smooth and economical to apply
Contains plastic
Excellent adhesion to all common surfaces
Resistant to water and alternating freezing/thawing
- Suitable for indoor and outdoor use
- Can also be used in wet rooms and swimming pools exposed to high stresses in conjunction with Würth compound sealant*
Tested in accordance with EN 13813
- Fire behaviour: Kl. A1/A1n
- Release of corrosive substances: CT
- Compressive strength: C25
- Tensile bending strength: F4
- Not suitable as a top surface without additional coverings or top surfaces!
- Be sure to add water in the appropriate quantities! Adding more water results in reduced strength and increased shrinkage. Such low-strength layers have a reduced load capacity, we therefore recommend removing them!
- Do not add water or fresh joint mortar to CERAfix 202 that has already started to harden to make it processable again. Loss of strength may result!
- The properties of the substrate are essential when it comes to ensuring the successful application of the product; the substrate therefore must be carefully prepared, cleaned and primed!
- If water is removed too quickly by e.g. room heating, strongly absorbent substrates, draughts, solar radiation etc. there is a risk of cracking!
- Ventilation of the installation location is necessary, however, draughts during processing and during the hardening process must be avoided as well as direct sunlight. The internal and floor temperature must be at least 5 °C during processing and for one week thereafter! Dehumidifiers must not be used in the first 3 days!
- Sulphite leaching adhesive or water-soluble floor covering adhesives must be completely removed!
- Largely remove old, water-resistant floor covering adhesives with tools. Small amounts of dispersion-based water-resistant floor covering adhesives (area percentage < 20 %/m², evenly distributed) can remain on the substrate. Clean the substrate and then prime it with CERAfix 103 or CERAfix 203, sprinkle with plenty of TEGAfix 430 quartz sand and vacuum after full reaction! Do not exceed a maximum single layer thicknesses of 20 mm!
- Not suitable for use on poured tarmac screeds!
- In the case of calcium sulphate screeds, the CM moisture content without underfloor heating must not exceed 0.5 % and with underfloor heating 0.3 % at the time of levelling with CERAfix 202. Thoroughly prime with CERAfix 103 or CERAfix 203 and sprinkle plenty of TEGAfix 430 quartz sand! After reaction has occurred (approx. 16 hours), sweep off and vacuum up the excess quartz sand. Then use CERAfix 202 to smooth up to a maximum layer thickness of 20 mm. Subsequent moisture ingress must be prevented.
- Contact between the cement-based mortar and the magnesite screed causes destruction of the magnesite screed by chemical reaction "magnesia expansion". Backwards moisture load from the substrate must be excluded by appropriate means. Magnesite substrates must be mechanically roughened and primed with epoxy resin CERAfix 103 or CERAfix 203. Spread plenty of fresh 0.5-1.0 mm grit quartz sand across the fresh epoxy resin layer. After approx. 16 hours* waiting time, further laying work can take place. Do not exceed a maximum single layer thicknesses of 20 mm!
- Edge, field, building and movement joints must be observed. These must be carried over or integrated at the specified location and suppressed with suitable means, e.g. edge strips! Dummy joints must be carved out once the CERAfix 202 has hardened up to a third of the applied layer thickness!
- Only use clean tools and clean water!
- To assess how mature the covering is, perform a moisture measurement using the CM unit.
- The technical data sheets of the products used must be observed!
- Protect surfaces that do not require treatment from exposure to CERAfix 202!
- Current applicable regulations must be observed!
For example:
- DIN 18157
- DIN 18352
- DIN 18560
- DIN EN 13813
- DIN 1055
- TKB information sheets from Industrieverband Klebstoffe e. V. (Industry Association of Adhesives)
- BEB information sheets, published by Bundesverband Estrich und Belag e. V. (Federal Association for Screeds and Coverings)
- Technical information "Interface coordination for heated floor structures".
- ZDB information sheets, published by the German tiling industry association.
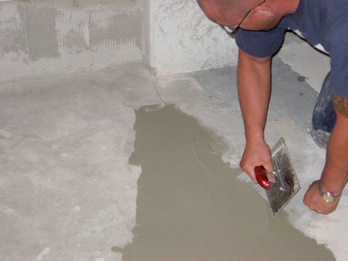
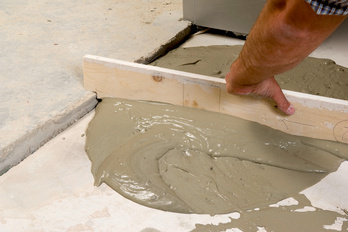
Datasheets(X)
CERAfix 202 is used for coating uneven concrete ceiling, wall and floor surfaces in accordance with DIN 1045, plaster from mortar class PII and PIII, masonry with heated and unheated cement screeds in accordance with DIN 18560 and fast cement screeds. CERAfix 202 is suitable for outdoor use, swimming pools, as well as in environments subjected to moisture together with a corresponding Würth compound sealant. CERAfix 202 is used in layer thicknesses of 2-20 mm.
- 1. The surfaces to be covered are generally primed with either CERAfix 101 or CERAfix 102 to a mixing ratio of 1:3 with water. Sand, clean and prime stable, ceramic coverings and smooth cementitious surfaces that are to be levelled with CERAfix 202 with CERAfix 103 or CERAfix 203. Spread with plenty of fresh 0.5-1.0 mm grit quartz sand. Mop and vacuum once cured!
- 2. Add 25 kg of CERAfix 202 to 4.7 to 5.0 l of water and mix to a clump-free, smooth and stable compound. We recommend using a Würth agitator with a speed of approx. 500-700 rpm. Give the product a short time to mature and then stir through again. Mixing time: approx. 3 to 5 minutes.
- 3. Then produce a contact filler layer with the material and spread on and/or actuate on the primed surface to the required coat thickness; level according to the levelling requirements.
- 4. Depending on the ambient conditions, the coat thickness and surface can be rubbed and smoothed with a damp sponge float after approx. 50-90 minutes. Additional coatings can be applied when the first coat is stable, but is still visibly moist. If the first coat appears to be dry, a second intermediate primer coat with CERAfix 101 or CERAfix 102 is required. Do not exceed a total layer thickness of 15 mm.
- 5. Hardening CERAfix 202 must be protected from quick extraction of water. e.g. through direct sunlight, high temperatures and draughts. CERAfix 202 can be covered with tiles and panels after approx. 4 hours*. For other surfaces, check the residual moisture using the CM device. When doing so, ensure that the permitted residual moisture content is observed in accordance with current technical leaflets. The CM measurement must be conducted in accordance with the current specialist information "Interface coordination for heated floor constructions"
Surface:
The base material must be solid, load-bearing, clean, dry and free from separating substances. Separating materials or layers, such as layers of sinter, dust, oil, etc., must be removed with suitable measures such as blasting, milling, suction and/or degreasing. Remove minimum-strength zones down to the stable core. The base material must have sufficient load-bearing capacity for the active loads - refer to DIN 1055. With screeds on separating or insulating layers, you need to check how mature the covering is before applying CERAfix 202 to prevent the screed panel from deforming further as a result of shrinkage processes. Shrinkage processes should be largely prevented. The CM moisture content must not exceed 2.0 CM% for cement screeds, 0.5 CM% for screeds on insulation or a separation breather and calcium sulphate screeds without underfloor heating, and 0.3 CM% for calcium sulphate screeds with underfloor heating. Subsequent moisture ingress must be prevented.
During application and in the week after, the air, material and base material temperature must be at least +5°C.
Chemical basis | Cement, mineral and polymer modified additives |
Min./max. processing temperature | 5 to 25 °C |
Max. processing time | 30 min |
Colour | Grey |
Mixing ratio | 4.7 - 5.0 l for 25 kg |
Full resilience | 28 d |
Container | Sack |
Shelf life from production | 12 Month |
Conditions to maintain shelf life from production | cool and dry storage area |
Application conditions | at 20°C and 65% relative humidity |
May be walked on after max. | 4 h |
May be walked on in following conditions | at 20°C and 65% relative humidity |
Can be covered after max. | 4 h |
Conditions for full resilience | at 20°C and 65% relative humidity |
Resistance against | Thawing-freezing alternations, Water |
Min. flexural strength | 4 N/mm² |
Conditions for flexural strength | after 28 days, 22°C and 65% relative humidity |
Min. compressive strength | 25 N/mm² |
Compressive strength conditions | after 28 days, 22°C and 65% relative humidity |
Application quantity in weight/area | 1.7 kg/m² |
Application quantity conditions | 0 - not applicable |
Permissible moisture content of levelling mass and cement-based base material is determined using the CM device | |||
Flooring | Heated | Unheated | |
Ceramic tiles or natural/artificial stone | Thick bed | 2.0 % | 2.0 % |
Thin bed | 2.0 % | 2.0 % | |
Water vapour diffusion-tight linings | 1.8 % | 2.0 % | |
Textile coverings | Blocks water vapour | 1.8 % | 2.5 % |
Permeable to water vapour | 2.0 % | 3.0 % | |
Parquet and laminate flooring | Floating installation | 1.8 % | 2.0 % |
The CM measurement must be conducted in accordance with the current work instruction FBH-AD from technical information "Interface coordination for heated floor constructions". |
Select RAL-colour code
!! NOTE: On-screen visualisation of the colour differs from real colour shade!!